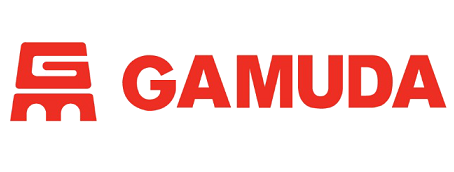
Gamuda Berhad Digitises Massive Jobsite with Viewpoint’s Field View™ Solution
Using Viewpoint Field View
In 1976, Gamuda Berhad started out as a small construction outfit, which steadily branched out into its three core businesses:
- Engineering and construction
- Property development
- Infrastructure concessions
As the company grew, its focus moved to larger transportation and infrastructure projects like highways and railways throughout Malaysia. Today, it is Malaysia’s largest civil engineering contractor, with expertise in project management, tunneling, geotechnics, engineering and construction.
Before
- Massive public transportation project designed around technology and innovation relying on manual processes in the field
- Disparate paper-based field data collection led to outdated or missing information across departments and projects
- Heaps of valuable data remained uncollected and subsequently unanalysed over the course of projects
- Lack of accountability control led to bypassed processes, potential quality issues and opportunities for theft and fraud
After
- Implementation of Viewpoint Field View™ drove digitisation of field data collection and provided real-time project information
- Increased visibility into the project and streamlined document management and collaboration across teams and processes
- Optimised forms fueled faster, more agile and accurate project information and project delivery
- APIs between Field View and business intelligence solutions increased ability of advanced data analytics
- Data tracking led to greater accountability with detailed audit trails, timestamps and digital signatures
Challenge
Gamuda’s reputation of expertise and innovation has not come without its challenges. As more large-scale projects coming into play in Malaysia, like the MRT Line 2 project, Gamuda sought to be on the forefront of new technologies to boost productivity and quality. The MRT Project is a highly complex endeavor, featuring both aboveground and underground sections. The aboveground section (38.7 kilometers in length) is into two phases. Below the surface, the project requires extensive underground tunneling — about 13 kilometres in length — and the construction of 11 underground stations.
The biggest roadblock the company faced was a notable absence of effective data collection in the field. “When I first joined, there wasn’t a construction document management system for a project this size,” said Tony Joseph, Gamuda’s development lead responsible for technology implementations and oversight. “It was kind of shocking.”
Permits, quality inspections, safety audits, defect tracking, site diaries and other documentation were all done with paper forms and tracking of documents and processes was limited at best.
“We had no idea how many documents had been lost in the past. We had no idea how many errors had occurred in the past. But we knew it is typical in construction to experience shortcuts, skipped inspections, and work completed without approvals,” said Ronan Collins, head of project information management for Gamuda.
One of the biggest problems with paper processes was the lack of up-to-date project data. “We’d get information that was two, three, four weeks out of date,” Collins said. This problem can become even worse when accurate contract sums are the name of the game. For instance, in tunneling: the power consumption (daily, per machine); the cost of replacement teeth on the cutter heads; the labor rates in comparison to actual rates being run on machines; all play an integral part in the success of the project and Gamuda’s bottom line.
“We had no idea what the actual rate of consumption was on a per-metre or -tunnel basis between different machines, because we just didn’t track the data,” said Collins. “But we knew we had to get better at that and provide answers for these scenarios.”
This is where the company decided to make major changes, and began looking for a solution to begin using for the tunnel portions of its MRT Line 2 project.
Solution
Collins said Gamuda initially began looking for an EDMS, or common data environment database in which it could standardise its data, documents and processes. The search led to Viewpoint for Projects, a document control solution for easily managing, accessing, and sharing large quantities of project documents. While researching that product, Collins said he and his team, including BIM Manager Nick Morecock, were introduced to Viewpoint’s Field View™ solution. As it turns out, Field View — a cloud-based and off-line mobile solution that digitises data collection in the field for quality, safety, project delivery and closeout/commissioning — was just the tool Gamuda needed. Morecock, a proponent of technology and driver of technology vendor relationships with the company saw a huge opportunity with Field View, Collins and Joseph said.
“It was kind of a no-brainer,” Collins said. “On construction jobsites, a lot of time tends to be wasted with people chasing around bits of paper, finding the right (documents) and getting the right people to sign off on them quickly. When we invested in Viewpoint for Projects, we made a proposition to the board of Gamuda that we should also invest in Field View in order to digitise the paper process on site.”
Field View, Collins said, was a very straightforward and easy to use solution, creating simple data collection and form workflows from the field to the office. “We knew it would be valuable, but we didn’t perceive just how valuable and effective it would be,” Collins said. “Everyone on-site, including our supply chain took to it quickly. It’s easy to use and saves a huge amount of time and hassle.”
Through Joseph, Gamuda identified a few “super users,” key engineers and department heads, to serve as drivers of the implementation of Field View. Together they set out on a mission to reduce reliance on paper by creating optimised digital site forms aimed to improve efficiency on-site. It took about six months for the Gamuda team to develop and streamline the 480 site forms/templates now used by more than 900 Field View users across many departments on the MRT Project. There are approximately 150 other users across the rest of Gamuda’s business units — a number Collins expects to grow.
Operating in the cloud, Field View fit with Gamuda’s tech-savvy operating style — many of its software systems and operations are cloud-based. “Security, backups, updates — all of that is handled by the cloud providers. [Cloud-hosting] allows us to move forward with the tools and functionality,” Joseph said.
Further leveraging the cloud, Gamuda is building powerful dashboards using the data collected from Field View and driving it to business analytic tools like IBM’s Cognos using APIs. “We’re basically building dashboards for the project managers and project directors to be able to review what’s happening in essentially real time,” Collins said. “It’s improving our use of Field View for collecting data, and then improving our engineers’ data literacy for reporting and project management.”
Gamuda was able to develop a streamlined safety plan for its tunneling operations using digital forms on-site and the dashboards detailing safety information in real time. “We’re doing the same for project management dashboards. Our ultimate goal is to use these for financial management, to monitor what’s completed and how much we’re paying our supply chain.” Collins said.
Results
In addition to boosting speed, productivity and access to critical project data it didn’t have before, Gamuda is realising a significant benefit in terms of project quality and accountability. Joseph noted it’s not uncommon in construction for submitters to make notes or sign off on items despite not being on-site.
“We also managed to track the actual time it takes for approvals and permits to be done. In previous cases, when a subcontractor was assigned, sometimes the work is done and then the permits are pulled. If you’re using a paper form, you can sometimes be very cheeky about things. You can always change the dates on a paper form, but with Field View, you can’t. Everything is tracked and logged,” Joseph said.
Field View improved jobsite security and helped save material costs as well. Joseph noted cases in the past where concrete “went missing” from delivery trucks either onsite or during delivery. “Now with digital forms, you’re able to trace the volume of concrete that reaches the site and the amount used versus delivered,” he said.
“And it wasn’t just concrete,” Collin added. “It was steel as well that was walking out of the gate…so it’s definitely improved the security in terms of the materials and equipment on site.”
With Field View fueling process digitisation on the MRT Project, Gamuda now plans to leverage Joseph and his team’s experience using Field View to expand use across other upcoming major Gamuda infrastructure projects.
“We’re working to make sure we standardise all of these forms, so no matter which project we’re on, the forms will look exactly the same. There’s been a lot of innovation with the MRT Project that we want to push across to the rest of the business,” Collins said.
“On the MRT project alone, we have created more than 200,000 live digital forms over the course of a year-and-a-half,” Joseph said, noting that of the 900 digital users, 200 are using tablets in the field, with the rest using smartphones.
The scale in which Gamuda is using Field View required some extra effort and attention from Viewpoint. Collins said despite some initial challenges with managing the amount of users Gamuda deployed in a short amount of time, Viewpoint stepped up and worked with its valued client to ensure success.
“We’re very happy with the support we’ve received. Viewpoint worked with us through our challenges,” Collins said. “We have no objections recommending Field View — especially for an industry that is coming together and embracing digitisation as it is now. I’m surprised more and more contractors aren’t already using it.”
A few of Gamuda’s recent project higlights:
- Work on the innovative Stormwater Management and Road Tunnel (SMART) in Malaysian capital Kuala Lumpur in which Gamuda’s own engineering division developed and executed a plan to merge a stormwater diversion channel with a double-deck motorway in a single tunnel, solving the capital city’s draining/flood mitigation and traffic problems.
- The stormwater tunnel project was also Malaysia’s first-ever use of a mixshield (slurry) tunnel boring machine (TBM), one of the largest in South East Asia at that time at 13.21m diameter, which received media attention from National Geographic.
- The conversion of 329 kilometres of the country’s single-track rail lines into double-track rail lines currently running the north-south axis of Malaysia.
- Work on the country’s Mass Rapid Transit (MRT) Line 2 project, an approximately 50 kilometre rail line connecting the communities of the greater Klang Valley traversing Sungai Buloh-Serdang and Putrajaya, in which Gamuda deployed the variable density tunnel boring machine, as the world’s first machine with the capabilities to not only drill into rock, but also soft grounds which permeate the Kuala Lumpur region.