5 Construction Workflows You Can Do Better This Year
0%
How to Simplify Everyday Construction Logjams—With a Little Help from Modern Tech
We’ve all heard the phrase, “New year, new me.” And if you’re like hundreds of thousands of individuals around the world, you probably started this year off with a laundry list of goals you set out to achieve throughout the upcoming year.
But did you make a list of workflows your construction organization can do better in the new year? If not, today’s your lucky day because we’ve made a list for you.
1. Mobile Time Entry and Payroll Review
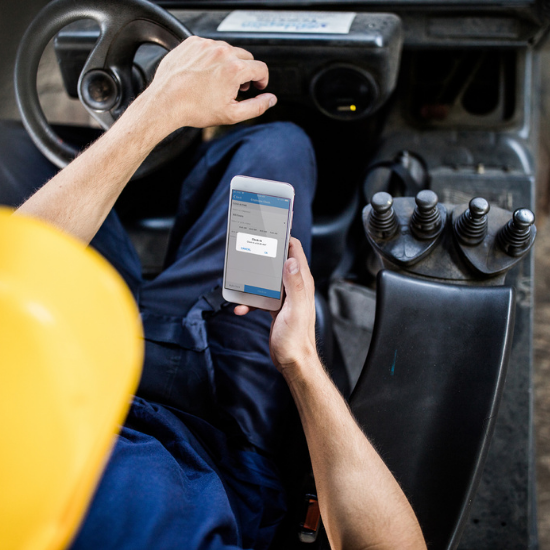
Time spent gathering and collecting paperwork for billing is a thing of the past. The manual processes required to manage paperwork for all employees, enter the data into the computer, and fix errors is a waste of time and money. As a result, office staff are unable to focus on higher valued tasks and if error occurs, employees risk not being paid on time. And that’s not good for anyone involved.
Thankfully, those processes are no longer necessary. With today's connected, cloud-based construction software, crews are able to enter their hours straight into the system without the help of office staff. This means that managers are able to approve payroll in real time, updating employee data in all connected software. By eliminating the need for double entry, the risk of error is decreased and employee data is consistently up to date. And in the end, employees are paid accurately and on time. It’s a win win!
2. Pending Purchase Orders
Time spent waiting for purchase orders to be approved can make or break the timeline of a project. When paperwork is passed off from person to person and questions arise, it can take days for final approval. And you don’t always have days to wait.
With the help of connected construction platforms, purchase orders are entered directly into the software from the field. From there, the review and approval process can immediately begin. The PO is then sent directly to the purchasing agent so no time is wasted. Through this simplified process, data entry is streamlined and time spent waiting on PO approval is minimized. With minimal errors or miscommunications, projects have a better chance of staying on track.
3. Field Purchase Orders
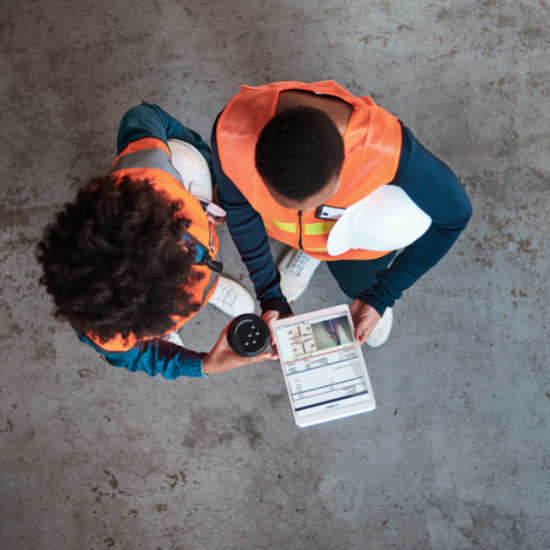
As we learned above, waiting on approval for purchase orders can result in massive project delays. From the initial request to the final PO being entered into the system, there are multiple opportunities for things to go wrong. Why wouldn’t you want to increase efficiency throughout this workflow?
Utilizing the right software can empower field crews to make quick purchases as needed. When parts or materials are purchased, a PO is automatically generated in the software system. The project accountant is then able to code the purchase to the proper project. With this streamlined process, your accounting teams are given more time to spend on more important tasks. And with easy-to-review audit trails, minimal time is spent looking back through old paperwork and files. And the best part? Software encryption works to keep your company’s data safe and secure.
4. Material Receipts
Managing materials and invoices are an important part of every project. As new material shipments arrive on site, the supervisor has to let the office staff know that the materials were delivered and ensure all paperwork makes it to the office. Those documents are then re-entered into the system so payments can be made and receipts can be stored. This can be a long and tedious process, but it doesn’t have to be.
Connected construction software simplifies the workflow for receiving materials. When items arrive on-site, supervisors can verify the shipment in the software. Received documents can be captured and uploaded directly into the system which allows for the auto-population of data. The AP department then has real-time access to these documents and is able to begin processing the payment. Not only does this allow for easy to track receipts and information, but it also keeps projects moving and crews well-informed.
5. Equipment Maintenance
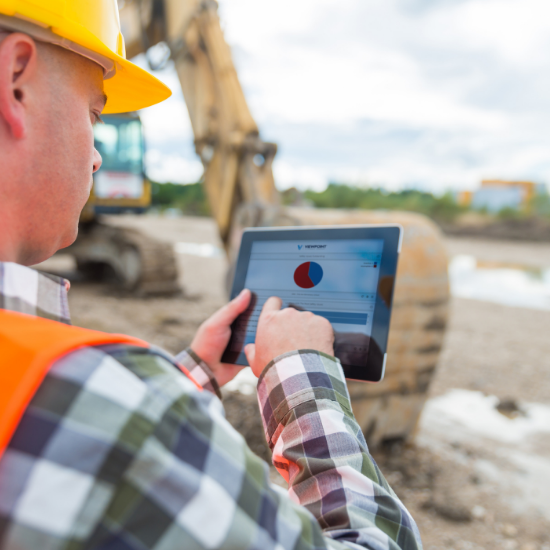
Unused equipment drains jobsite profitability. And what usually causes a piece of equipment to go unused? Equipment damage or needed maintenance. When equipment is in need of maintenance, project schedules are impacted. While there may be a schedule in place to monitor the maintenance schedule, parts inventory, mechanic’s time, etc., the manual time required drains efficiency.
To help make this workflow easier, construction software streamlines equipment management tasks and helps you find the “equipment management sweet spot.” Each piece of equipment is entered into the software to allow for proper tracking of maintenance needs and scheduling. The system works to ensure each piece of equipment is properly maintained. When it comes time for maintenance, all the equipment manager has to do is initialize a work order and assign the work to a mechanic. From there, the mechanic has the ability to update the work order, enter information and transfer the documents back to the manager. Through this increased efficiency, overall project productivity is increased.
What better way to start off the new year than to implement these streamlined workflows within your organization? We hope that in addition to your own personal goals, we can play a part in achieving your construction business goals as well.
If you’re looking for the perfect connected construction software to get the ball rolling, be sure to check out Trimble Construction One.